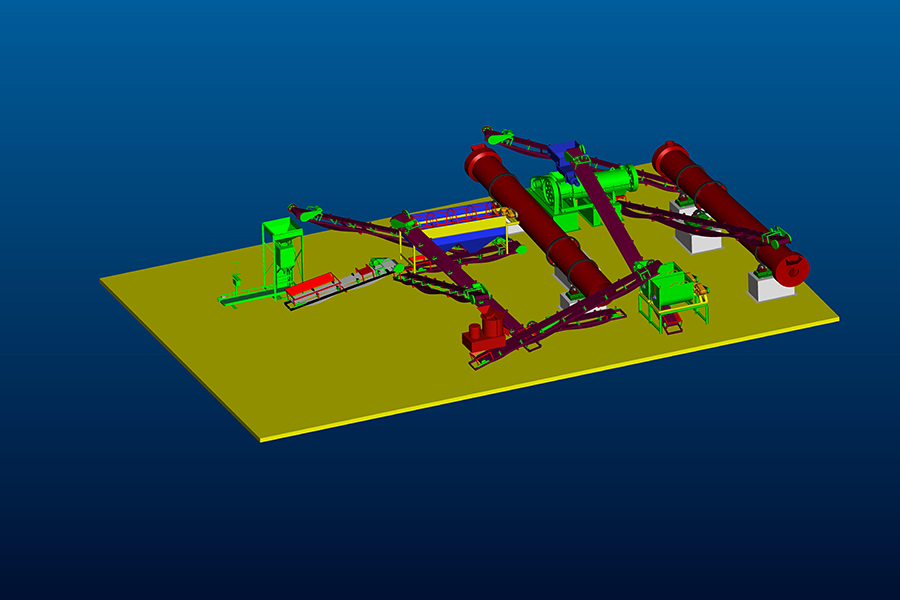
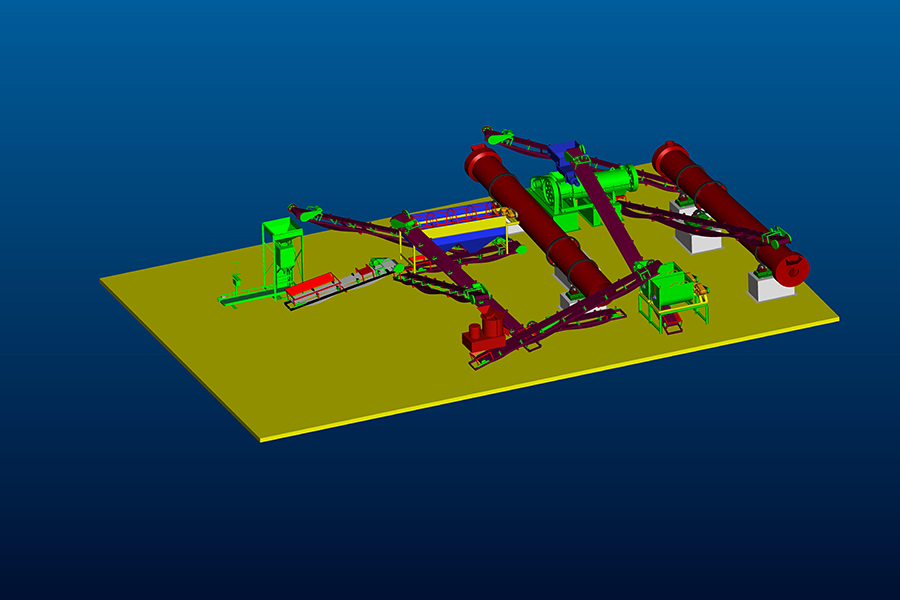
NPK Fertilizer Production from Superphosphate
- Production Capacity: 10,000 to 200,000t Annually Organic NPK Fertilizer Production
- Turnkey Project Solutions:Provided
- Customized Services:Provided
- Installation:Provided
- Main Equipment:Grinder, Blender, Conveyor, Granulator, Dryer and Cooler, Coater, Packer, etc.
Get Price Now!
Description
At present, the production of compound fertilizer with superphosphate as raw material occupies a considerable proportion. Many factories use superphosphate, urea, ammonium sulfate, potassium chloride, etc. as raw materials to make ternary compound fertilizers.
The main components of compound fertilizers made from basic fertilizers such as superphosphate, ammonium sulfate and potassium chloride are: urea, urea ammonium phosphate, ammonium gypsum, potassium gypsum and other double salts, as well as potassium ammonium chloride, potassium ammonium sulfate, ammonium phosphate Potassium, ammonium potassium gypsum and other solid solutions.
How to make npk fertilizer from superphosphate?
-
Pre-drying of superphosphate
The produced superphosphate generally contains 10% to 15% free water. It is difficult to pulverize superphosphate with such a high-water content, and it is difficult to find a suitable pulverizer. Therefore, it is best to pre-dry the superphosphate to reduce the moisture content to less than 5%. The superphosphate pre-drying method can usually be directly heated by co-current flue gas, the temperature of the flue gas is 400~550℃, and the temperature of the material outlet is 75~85℃.
-
Crushing of raw materials
If the raw materials for the production of compound fertilizer (superphosphate, urea, potassium chloride, etc.) are not pulverized, the particles will be large, the granulation will not be good, and the fertilizer mixing will be uneven, which will directly affect the quality and appearance of the compound fertilizer. Therefore, before granulation, it must be pulverized separately to ensure that the particle size of various materials is less than 1mm.
Superphosphate and urethral cord can be crushed by chain or hammer mill. Urea cannot be pulverized with a high-speed pulverizer, in order to avoid high temperature, high viscosity of the material and poor pulverization effect. Potassium chloride can be pulverized by a high-speed fertilizer pulverizer or a chain pulverizer. The crushed materials are preferably screened by a vibrating screen, the materials smaller than 1mm are used for mixing and granulation, and the materials larger than 1mm are returned to be crushed again.
-
Ammonation of superphosphate
Since the superphosphate produced by the current phosphate fertilizer plant contains 4% to 5% of free acid (H3PO4), if no pretreatment is carried out, various reactions will occur during the fertilizer blending process, which will affect the fertilizer granulation process. The essence of the pretreatment process is the process of neutralizing the free acid with a neutralizing agent. After neutralized superphosphate, free water becomes crystal water, and the obtained material has low solubility, which is beneficial to the granulation of mixed material. Most manufacturers of neutralizers use ammonium bicarbonate, so the process is called ammoniation. Ammonia, ammonium sulfate or calcium magnesium phosphate fertilizer can also be used as neutralizing agent, but because ammonium bicarbonate is convenient in source and cheap in price, using it as neutralizing agent can better meet the production requirements.
With the deepening of the degree of ammonification, calcium dihydrogen phosphate, phosphoric acid, etc. undergo a series of chemical reactions with ammonia, which reduces the content of water-soluble phosphorus pentoxide and available phosphorus. Therefore, superphosphate ammoniation must be strictly controlled, and it should not be excessive, otherwise it will affect the quality of compound fertilizer.
-
Mix
Mixing is to transport the three main basic fertilizers of nitrogen, phosphorus and potassium into the mixer according to the prepared formula. The mixers are available with drum or vertical discs. The mixing must be sufficient, and it should be used immediately after mixing. It should not be placed for too long after mixing to avoid moisture. For the mixer with D = 2000mm, the appropriate speed is 24~30r/min, and the mixing time is about 30min.
-
Granulation
(1) Agglomeration method
The granulation process is the key process of compound fertilizer production. Regarding the basic principle of granulation, the National Fertilizer Development Center (NFDC) of the United States and ICI Company of the United Kingdom have proposed the principle of particle growth based on the liquid phase theory, which can be used as the theoretical basis for the agglomeration and granulation method.
Using the liquid phase coefficient, the total liquid phase of the formulation can be determined. The total liquid phase amount is well controlled, and the granulation effect is usually good.
The temperature and the amount of returned material also have a certain influence on the granulation quality, and the temperature affects the solubility of each material. The relationship between temperature and water content can be expressed by the following empirical formula:
t= 104.9-4.04x
formula:
t: granulation temperature, °C;
x: Moisture content of qualified granular materials exported from the granulator, % (mass).
It can be seen from the above formula that the higher the moisture content of the material, the lower the temperature required for granulation; on the contrary, the lower the moisture content of the material, the higher the temperature required for granulation. The reason is that when the water content of the material is high, the amount of liquid phase required for granulation is sufficient, and there is no need to increase the amount of liquid phase by increasing the temperature to increase the solubility of soluble salt; when the water content of the material is low, it is necessary to increase the temperature. The solubility of water-soluble salts can increase the amount of liquid phase to meet the requirements of granulation.
In the granulation method with return material, the amount of return material is related to the water content of the material. When the water content is low, the amount of returned material is less; when the water content is high, the amount of returned particles is more. Due to the high temperature of the returned material, it can also play a role in adjusting the temperature.
Granulation is carried out in a granulator. The material mixed by the fertilizer blending equipment is transported into the granulator, and an appropriate amount of binder is added. The material is turned and rolled by the granulator, and gradually grows into granules.
The quality of the granulation effect mainly depends on the design and operation of the granulator, the inclination angle, rotation speed, diameter of the granulator, the concentration and dosage of the binder, and the feeding and discharging methods.
For the disc pan plate granulator, sulfuric acid or phosphoric acid is generally used as a binder, and the concentration of sulfuric acid can be about 50%. The amount of binder generally depends on the size of the particles. If the amount of binder added is large, the balls are usually formed quickly and the particles are large. Generally, 1t of compound fertilizer is produced, and about 50kg of 98% (mass) concentrated sulfuric acid is used. The inclination angle of the disc granulator is generally 45°, the rotating speed of the disc is 30r/min, and the diameter of the disc is 1.6~2.2m. Commonly used disc granulator, the relationship between its specifications and production capacity is shown in Table 2-35.
Disc Diameter | ф 1600mm | ф2000mm | ф2200mm |
Disc Height | H300mm | H240mm | H360mm |
Rotating Speed | n: 19r/min | n: 30r/min | n: l4r/min |
Installation Angel | a =45∘ | a =60∘~ 65∘ | a=35∘~ 55∘ |
Production Capacity | 0.6-1.6t/h | 1.5-2t/h | 6t/h |
The area under the disc with a radius of 3/4 is automatically discharged. Continuous mechanical feeding, the feeding is kept stable, and the material is added from the upper position deviating from the vertical line by 45°. To stabilize the moisture content of the material, use an appropriate amount of adhesive to maintain the appropriate viscosity of the material, and at the same time, the disk surface should be cleaned frequently to ensure effective rolling of the particles in the disk. The rotation speed should be selected so that the material has enough rolling area and corresponding stay time. The diameter of the granulating disc is 2200mm, the feeding rate per hour is 4t, and 24r/min is more suitable. The amount of adhesive added should be controlled so that the material has a higher granulation rate, so as to avoid the increase of the return material and increase the consumption in the production process. In order to reduce the drying load and reduce the drying temperature of the product, the moisture of the material should be controlled to a minimum during granulation, which requires increasing the granulation temperature during the granulation process to reduce the granulation moisture. To increase the granulation temperature, steam heating or pretreatment can be used, or the chemical reaction heat of the process can be utilized.
(2) Extrusion granulation method
This method is a granulation process in which materials are directly extruded into finished products, and is especially suitable for granulation of heat-sensitive materials. The extrusion granulation method can be regarded as a granulation process without chemical reaction by adding steam to dry materials. Its main features are to reduce energy consumption and simplify the process flow. Since the product is always dry, the drying and cooling steps of the agglomeration method can be omitted, nitrogen losses are avoided, and there is no problem of pollutants polluting the environment.
Extrusion granulation is carried out in an extruder, and its working principle is as follows:
The vertical shaft rotates at a certain speed, driving the four rollers fixed on the vertical shaft to revolve around the vertical shaft.
The center line revolves, and the rollers rotate around their own central axis at the same time. The pre-adjusted working gap is always maintained between the four rollers and the template, and small through holes are evenly distributed on the template. well-mixed
The material is continuously and quantitatively sent to the upper cylinder of the granulator through the feeding device. Using the affinity between the material molecules, under the forced extrusion force between the roller and the template, the material is placed on the template.
The small hole is rubbed, compressed and extruded to form a cylindrical shape. Then through the shearing force of rotation, it is cut into the desired short cylindrical particle shape.
NPK Extrusion Granulation Process
Calcium pretreatment-Processed Calcium, Nitrogenous Fertilizer, Potassium Fertilizer calculation-Mixing-Granulation  -Packaging.
The key to using extrusion granulation is to control the feed moisture, generally 6% to 8%, mainly refers to the pretreatment of superphosphate. – The superphosphate must be dried, crushed, sieved and ammoniated. Other basic fertilizers such as urea, ammonium sulfate, ammonium chloride, potassium chloride, etc., can be directly sent to the extrusion granulator for processing without further crushing.
Before the material enters the extruder, it is best to perform magnetic separation to remove the entrained material in the material.
Iron filings and other impurities, so as not to damage the machine.
The feed of the extrusion granulator is monitored by the stability of the ammeter pointer of the electrical control cabinet. In use, it should be noted that the physical and chemical properties of each single basic fertilizer are different, and the load current during extrusion granulation is also different. Before each shutdown, the compound fertilizer in the machine should be extruded. After the current value is greatly reduced, the easily decomposable basic fertilizers such as urea and ammonium bicarbonate can be pressed into the small holes of the template, and the machine can be used directly next time.
In the extrusion granulation process, two basic fertilizers, superphosphate and urea, cannot be used for production. Because superphosphate contains free acid, a chemical reaction occurs with urea during extrusion.
Due to the precipitation of water during the reaction process, the material becomes thin, moist and sticky. At the same time, the decomposition rate of urea increases, making granulation impossible. Therefore, calcium magnesium phosphate fertilizer or other fertilizers, such as potassium sulfate, potassium chloride, etc., must be added in the formula.
(3) Shotcrete granulation method
The spraying method is to spray the slurry through a nozzle into small droplets, which are dried and cooled to make qualified smooth spheres. Slurry granulation can be carried out in a circular cylinder or a tower. The ejected droplets and the rising gas meet in opposite directions, and mass transfer and heat transfer are carried out at the same time, and the droplets are dried and cooled into solid particles.
The amount of material returned in the shotcrete production process depends on the nature and water content of the treated slurry, and is generally 2.5 to 3.0. The return material is guided through the return pipe, and it is better to guide the return material into the vortex of the high-speed furnace gas, so that it can be strongly mixed with the return material of the slurry, give full play to the function of the return material, and reduce the amount of the return material. Shotcrete granulation is mainly used in the granulation of nitrophosphate fertilizer or ammonium phosphate, and is less used in the production of compound fertilizer with superphosphate as raw material.
Economic comparison of three granulation methods
At present, the total annual output of chemical fertilizers in the world is about 400 million tons, and about 136 million tons in terms of nutrients (N+ P205+ K20), of which about 50% of the products are made into pellets. The particle size of various granular products actually varies greatly depending on the production method and region (market demand), but in most cases, the particle size range of granular fertilizers is generally between 1 ~ 4mm.
Most of the multi-component (NPK) fertilizer products (about 60 million tons/year, excluding binary compound fertilizers such as ammonium phosphate), which account for about 15% of the world’s fertilizer production, are produced by the above three basic granulation methods. Economic comparison of several process methods.
The comparison is mainly made on (1) fixed capital investment, (2) processing cost (excluding raw materials) and (3) production cost (processing cost and processing raw material cost). The main economic features are discussed.
The estimated fixed capital investment for the three production scenarios, of which the agglomeration equipment is the lowest, is $3.2 million. Shotcrete granulation was the highest at $16.4 million. Storage facilities in the former account for about 65% of total fixed capital investment.
However, the storage facilities of extrusion granulation and shotcrete granulation devices with higher investment costs only account for 20% to 24% of the total investment.
Estimation of processing costs (excluding raw material costs) for three NPK production methods. Processing costs are based on annual 120,000 tons of product, including bagging, but excluding raw material costs. The highest processing cost is: 20 USD/t for the agglomeration method, 35 USD/t for the extrusion method, and 52 USD/t for the shotcrete method. Regardless of the method, among the fixed processing costs, the fixed investment recovery (calculated based on the service life of 15 years and the annual interest rate of 15%) accounts for the highest proportion.
The cost of raw materials processed by the three granulation methods is calculated based on the most common NPK compound fertilizer 15-15-15 product in the international market. It can be seen from the table that the agglomeration method is the highest at US$139/t, and the extrusion granulation method and the shotcrete granulation method are 1~12 US dollars/t lower than the disc agglomeration granulation method.
Coating treatment
After the granulated compound fertilizer is granulated, it is best to be treated with coating powder to improve the physical properties of the surface of the granules, so as to maintain the quality of the finished product during storage, without caking, moisture, good strength and good hand feel.
The dusting process is to add dusting powder to the finished product, roll it properly, and let it mix evenly.
Dusting agents are usually clay, calcium magnesium phosphate fertilizer, gypsum powder, talcum powder, etc. The general dosage of dusting agents is 2% to 4% of the amount of compound fertilizers. The main chemical compositions of commonly used dusting agents are shown in Table 2-40.
Key Fertilizer Granulators Used in the NPK Compound Granulation Plant
-
Disc granulator
Figure 2-10 is the basic structure of the disc granulator. The disc granulator is currently the most used granulation equipment by compound fertilizer manufacturers. It has the advantages of simple structure, low cost and convenient maintenance.
The disc granulator is composed of a shallow tray with an angle and a support frame, and its inclination and the rotation speed of the disc are adjustable. The mixed materials in the mixer are sent to the top of the disc granulator by a belt conveyor, and are continuously and quantitatively fed into the disc. As the disc rolls over, the particles gradually grow up. Due to the remarkable classification capacity of the disc granulator, the large particles float on the top and are continuously discharged from the bottom of the disc, while the smaller particles remain in the disc with the new ones. The added material sticks together and continues to grow. The granulation of the disc granulator is very uniform, and the material returned is very small, and its production capacity is large. One ordinary disc granulator can produce 4t of finished products per hour.
The disc granulator is mainly divided into two parts, one is the disc (including the round weir, the general weir height is 0.1~0.25D), and the other is the transmission machinery. The disc has a certain inclination angle, generally 45°~60°, and the rotational speed is 30r/min.
The disc granulator has the following characteristics:
 it has a good grading effect, and generates less coarse particles, so the granulation rate is high; the entire operation process can be observed, and problems in the operation can be found and adjusted in time; It has great flexibility and a wide range of particle size control; it is widely used because of the simpler equipment and less investment. The equipment cannot carry out ammoniation treatment on materials, and it is difficult to collect dust and smoke.
Rotary Drum Granulator for NPK Fertilizer Production Plant
Figure 2-11 is a schematic diagram of the drum granulator. The main granulating part is an inclined rotating cylinder, there is a retaining ring at the inlet to prevent the feed from overflowing, and there is also a retaining ring at the outlet to ensure the depth of the material layer. The materials mixed by the mixer blender are automatically quantitatively fed into the cylinder drum and contact with the sprayed droplets.
Due to the continuous tumbling of the drum, the material gradually becomes a ball, and the material is continuously added.
Granules are continuously discharged and continue. The inner wall of the cylinder is equipped with a scraper to prevent the material from sticking to the barrel wall.
The general specification of the drum granulator is φ1000 x 2000mm, and the production capacity is 5000t/a
The rotary drum granulator increases the liquid phase content in the granulated material by the granulation temperature, promotes the material to be granulated at a lower water content, provides convenience for drying, and significantly reduces energy consumption.
Suitable process conditions for drum granulator:
- Material residence time: 3 ~ 5min
- Speed: 16r/min
- Granulation temperature: 50~55℃
- Ton fertilizer consumption index:
- Coal: 500kg
- Steam: 53kg
- Electricity: 54kWh
-
Extrusion granulator
The working principle of the extrusion granulator is shown in Figure 2-7.
In addition, there is a roller extruder, which is installed by two rollers side by side with a small distance. Generally, one roller is fixed and the other is rotated relatively. When the material passes through the middle of the roller, the whole sheet is extruded. The prepared large billet is broken into small pieces in the lower part of the extruder.
Another type of extrusion process is to compact the material between two rollers with symmetrical dimples on the surface to produce spherical particles. Foreign compaction can produce 1.2~3.3mm particles. In China, 6, 8, 12mm spherical compound fertilizers can be produced by this extrusion process.
At present, the extrusion granulator made in my country is used, and multiple sets can be installed according to the production capacity. The specifications, models and main technical parameters are as follows:
Name: Multifunctional double roller extrusion granulator machine
- Specifications: The aperture of the synovial membrane is φ2.5mm, medium 3.5mm
- Main technical parameters: speed 192r/min
- Output: 1t/h
- Main motor model: JXJ111-35LW0.6kW
- Discharge temperature: 25~45℃
Before use, close the blanking control board, and then the conveyor will send the evenly stirred materials to the blanking box. After starting, the blanking control board will be pulled away for feeding. If the operation fails, stop the machine immediately and clean it up in time to prevent the material in the machine from being hardened and blocked, which will affect the use. There are some fine particles or powders coming out of the extrusion granulator, which can be returned to re-granulation.
The general process of superphosphate production of compound fertilizer
The general process of producing compound fertilizers based on superphosphate, urea, potassium chloride, etc., is shown in Figure 2-13.
After the superphosphate is pulverized, it is mixed with ammonium bicarbonate for ammoniation, and then enters the dryer for drying, so that the moisture content of the material is reduced to less than 5%. Then it is screened, the coarse material is returned to the pulverization process, and the fine powder is mixed with urea and potassium chloride, conveyed through a belt, and continuously enters the pelletizer, and is added with a binder for granulation. The granular fertilizer that comes out is dried, cooled and sieved, and the coarse and fine particles are used as return material. The qualified particles screened out in the middle layer enter the finished product hopper, are bagged by the automatic packaging machine, and sent to the finished product warehouse.
The main equipment of the compound fertilizer production line with an annual output of 20,000 tons is: 1 set of φ2000x 14000x12mm SSP dryer; 1 set of φ1850 x 8000 x 12mm drum granulator, motor 7.54kW; 1 set of φ1200x 10000x 12mm finished product dryer, motor 7. 5kW; φ1000x 3700mm rotary screening machine – one, motor 4kW; there are more than 20 sets of fertilizer pulverizers, dust removal equipment, coolers, induced draft fans, water pumps and other equipment.
Costs on NPK Fertilizer Production from superphosphate(1t/h)