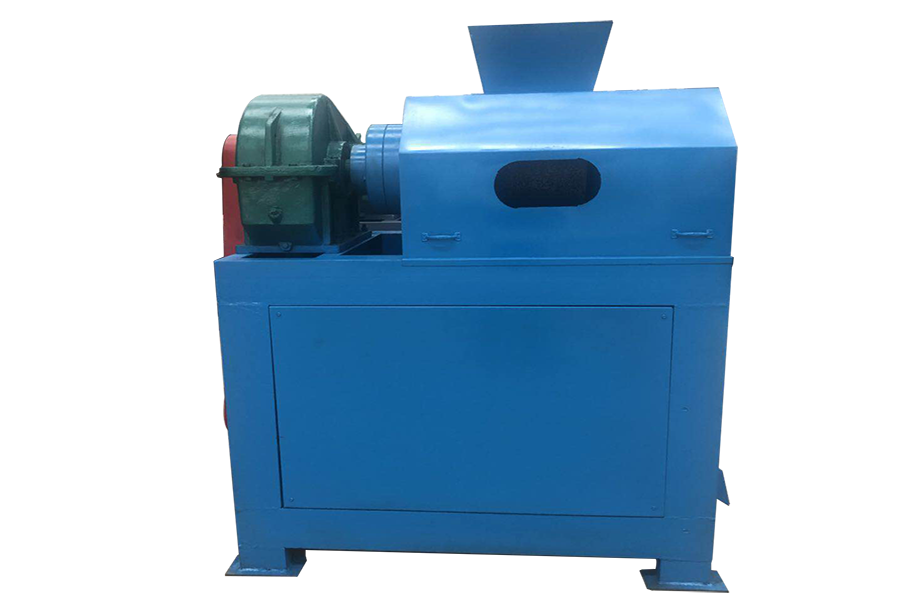
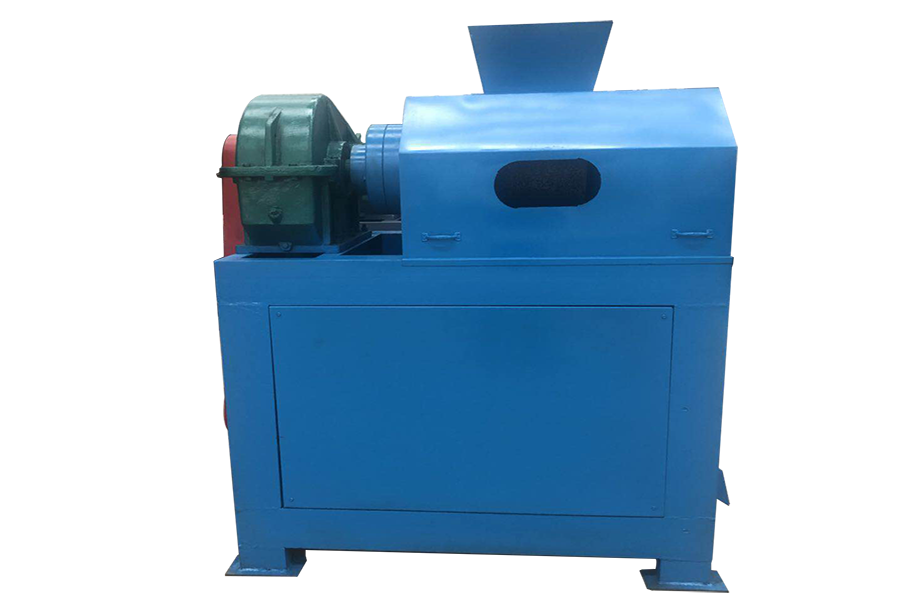
New Developed Extrusion Granulator
- Output (kg/h): 5000
- Voltage: 380/400/440/600
- Dimension(L*W*H): ACCORDING TO DRAWING
- Usage: Producing NPK Compound Fertilizer Granules
- Raw Material: Compound Fertilizer
- Applicable Industries: Manufacturing Plant, Farms, Construction works, Energy & Mining
- Core Components: PLC, Engine, Bearing, Gearbox, Motor, Pressure vessel, Gear, Pump
Get Price Now!
Description
The new type of double-roll extrusion granulator is a new type of organic fertilizer granulation equipment after many improvements have been made on the basis of the original double-roll extrusion granulation machine. The kinetic energy transmission is increased to the five-slot V-belt to transmit kinetic energy, which fully transmits the power of the motor and reduces the kinetic energy loss.
The reducer adopts the company’s research and development design, with high transmission efficiency and stable kinetic energy.
The feeding port is equipped with a designed feeding stirring mechanism to ensure that the material can enter the roller skin mold evenly and prevent the feeding port from being blocked.
The mold-to-shell adjustment adopts a spline-type adjustment and fixing mechanism.
Both sides of the lower end of the roller skin mold are equipped with automatic cleaning scrapers to prevent the material from sticking to the roller skin.
How does the new developed extrusion granulator work in the granulation process?
The working principle is: the belt and pulley are driven by the motor, transmitted to the driving shaft through the reducer, and synchronized with the driven shaft through the split gear to work in opposite directions. The material is added from the feeding hopper, extruded by the rollers, demolded into balls, and passed through a pair of chains, sent to the crushing screen studio, screened and separated the finished granules (balls), and then the returned material is mixed with the new material, Granulate again. With the continuous rotation of the motor and the continuous entry of materials, mass production can be realized.
Applicable materials for the new type extrusion granulator machine
Ammonium bicarbonate, urea, ammonium chloride, ammonium phosphate, potassium chloride
Technical Specifications for the new deigned npk dry extrusion machine
How to make quality fertilizer pellets with the new type roller extrusion granulator?
The adjustment of the roller gap of the roller extrusion granulator directly affects the use effect of the granulator. It should not be too large or too small. So how much is appropriate to adjust, and what are the specific operation steps? The following will give you a detailed answer:
The new type of roller extrusion granulator has the characteristics of low energy consumption, high energy saving, low investment and simple operation. The roller extrusion granulator produced by us has been debugged before leaving the factory. After the customer purchases the granulator, it needs to be adjusted before use. After a period of use, due to roller wear and poor granulation effect, it is necessary to adjust the roller squeezes the gap of the granulator.
The correct method should be adopted when adjusting: first, the interval between the pressure rollers should not be too small or too large, and must be adjusted within the specified range; secondly, the pressure cover on the bearing seat side should not be too loose or too tight, the bearing roller will offset.
Advantages of the new type of roller extrusion granulator
- Low energy consumption and energy saving granulator Extrusion granulation is a material granulation method at room temperature. Compared with other methods, it does not require drying methods such as fuel and gas.
- Steam granulation is a commonly used method for producing compound fertilizers without adhesives in China. Through intermolecular condensation and crystallization, steam plays a binding role in the production process. However, during the drying process, the water inside and on the surface of the granules must be drained, otherwise, the fertilizer will easily stick to the clumps during storage. Dry granulation does not require another additive, just use the intermolecular force of the material itself to simplify the process and reduce energy consumption.
- Because the drying process saves cost, has low return (about 15% of the total extruder consumption), simple process and low investment, the investment is low.
- The materials used in the extrusion granulator include more than 20 kinds of materials such as ammonium nitrate, urea, ammonium chloride, calcium nitrate, potassium chloride, potassium sulfate, etc., and the extrusion granulation process can flexibly change the product formula in a short time. A set of equipment can produce up to 30 kinds of formula products.
Get a Free Quote with Detailed Price Lists, Inquiry Us Now